Leading Approaches for Optimizing Steel Manufacture Processes for Optimum Performance
From careful layout intending to accepting cutting-edge modern technologies, the quest for optimal effectiveness in steel manufacture includes a complex technique. Allow's check out just how these techniques can revolutionize steel construction procedures, paving the means for unprecedented performance and competitiveness in the market.
Reliable Layout Preparation
In the realm of steel construction procedures, efficient and tactical format planning plays an essential duty in improving manufacturing operations and maximizing operational efficiency. The format of a steel fabrication facility straight influences the efficiency of operations, material circulation, and employee productivity. By thoroughly creating the setup of equipment, workstations, storage areas, and material handling devices, firms can significantly decrease unnecessary motion, lessen product taking care of times, and optimize the total manufacturing process.
An effective format plan takes into consideration aspects such as workflow sequences, proximity of workstations, product handling routes, and security policies. It aims to create a streamlined and sensible flow of activities from resources intake to the end product dispatch. Through effective layout planning, firms can remove traffic jams, lower manufacturing downtime, and boost the general operational performance of the steel manufacture procedure.
Moreover, a well-balanced design plan enables better application of readily available room, enhanced communication between employees, and improved security practices within the center. On the whole, spending time and resources in developing a reliable design plan can yield significant advantages in terms of raised performance and cost savings for steel manufacture services.
Advanced Cutting Technologies
Using sophisticated modern technologies in steel manufacture processes improves accuracy, effectiveness, and general manufacturing top quality. In addition, plasma reducing modern technology has actually additionally changed steel manufacture by making it possible for swift and specific reducing via electrically conductive products. By integrating these sophisticated cutting innovations into steel fabrication processes, manufacturers can significantly increase performance, lower manufacturing times, and eventually improve the quality of their products.
Automated Welding Equipments
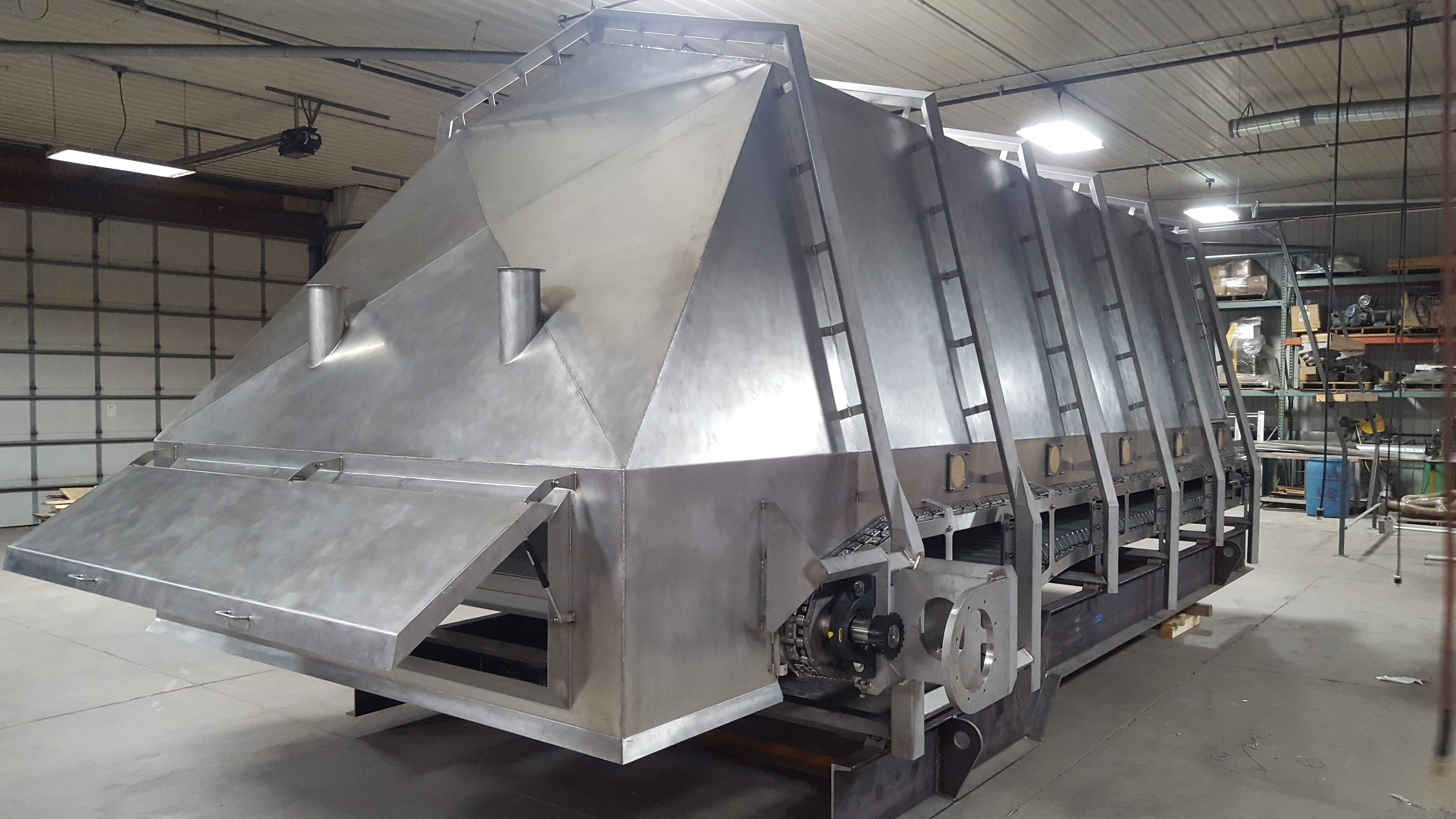
One of the vital advantages of automated welding systems is their capacity to preserve a high degree of accuracy throughout the welding procedure. The precision used by these systems ensures that welds are consistent and fulfill the required specs, resulting in more powerful and more trusted metal frameworks. Additionally, automated welding systems minimize the threat of human error, leading to less problems and revamp.
Furthermore, these systems can manage intricate welding tasks easily, consisting of welding in tight areas or on bent surface areas. This flexibility makes automated welding systems appropriate for a large range of steel construction applications, from large industrial projects to elaborate personalized layouts. In general, the application of automated welding systems in steel manufacture procedures significantly improves effectiveness, high quality, and total task outcomes.
Stock Administration Solutions
Enhancing functional effectiveness and enhancing procedures, reliable stock administration options play a critical duty in maximizing steel manufacture procedures. By applying durable stock administration systems, steel construction companies can guarantee that the right materials are readily available when required, decreasing interruptions and delays in production schedules. Making use of innovative software application options enables for real-time tracking of supply degrees, allowing accurate projecting of product demands and preventing stockouts or overstock scenarios.
In addition, stock management remedies aid in official site decreasing carrying prices related to excess stock and boost money flow by straightening stock degrees with real demand. By classifying materials based upon usage regularity and urgency, fabricators can focus on procurement and storage room allotment, further boosting operational performance. Additionally, applying barcode or RFID innovation facilitates precise inventory monitoring and simplifies the tracking of material activities within the facility.
Continual Process Improvement
To build on the gains made through reliable inventory management options, the emphasis now changes towards driving constant procedure enhancement within steel manufacture operations. Constant procedure improvement is a methodical additional reading approach targeted at boosting efficiency, minimizing waste, and raising overall high quality throughout the manufacture process. By carrying out a society of continuous improvement, steel construction firms can identify bottlenecks, improve operations, and maximize resources to optimize performance.
One key aspect of constant procedure renovation in steel manufacture is the routine review and analysis of production processes. This includes celebration responses from staff members, monitoring essential performance signs, and determining areas for enhancement. By leveraging data-driven insights, business can make educated decisions to drive significant modifications that positively affect operations.
Furthermore, embracing lean manufacturing principles can considerably contribute to process improvement in steel manufacture. steel fabrication Get More Information melbourne. Methods such as value stream mapping, 5S organization, and Kaizen occasions can aid remove non-value-added tasks, standardize processes, and foster a society of advancement and constant discovering within the organization
Final Thought
To conclude, optimizing steel construction procedures for maximum effectiveness needs mindful planning, using innovative reducing technologies, executing automated welding systems, taking care of inventory efficiently, and constantly boosting procedures. By incorporating these techniques, makers can boost performance, reduce expenses, and improve general efficiency in the steel manufacture sector.
Via effective layout planning, business can get rid of bottlenecks, minimize manufacturing downtime, and boost the total functional efficiency of the steel fabrication process. steel fixing.
Making use of cutting-edge modern technologies in steel fabrication processes enhances precision, effectiveness, and overall manufacturing high quality. By integrating these advanced reducing technologies right into steel manufacture processes, manufacturers can dramatically boost effectiveness, reduce manufacturing times, and eventually boost the high quality of their products.
In general, the implementation of automated welding systems in steel fabrication procedures dramatically enhances effectiveness, quality, and total task results.
One key facet of continual procedure renovation in steel construction is the regular review and evaluation of production procedures. (Alpha reo)